How Often Should A Hoist Be Serviced (Rules and Regulations)
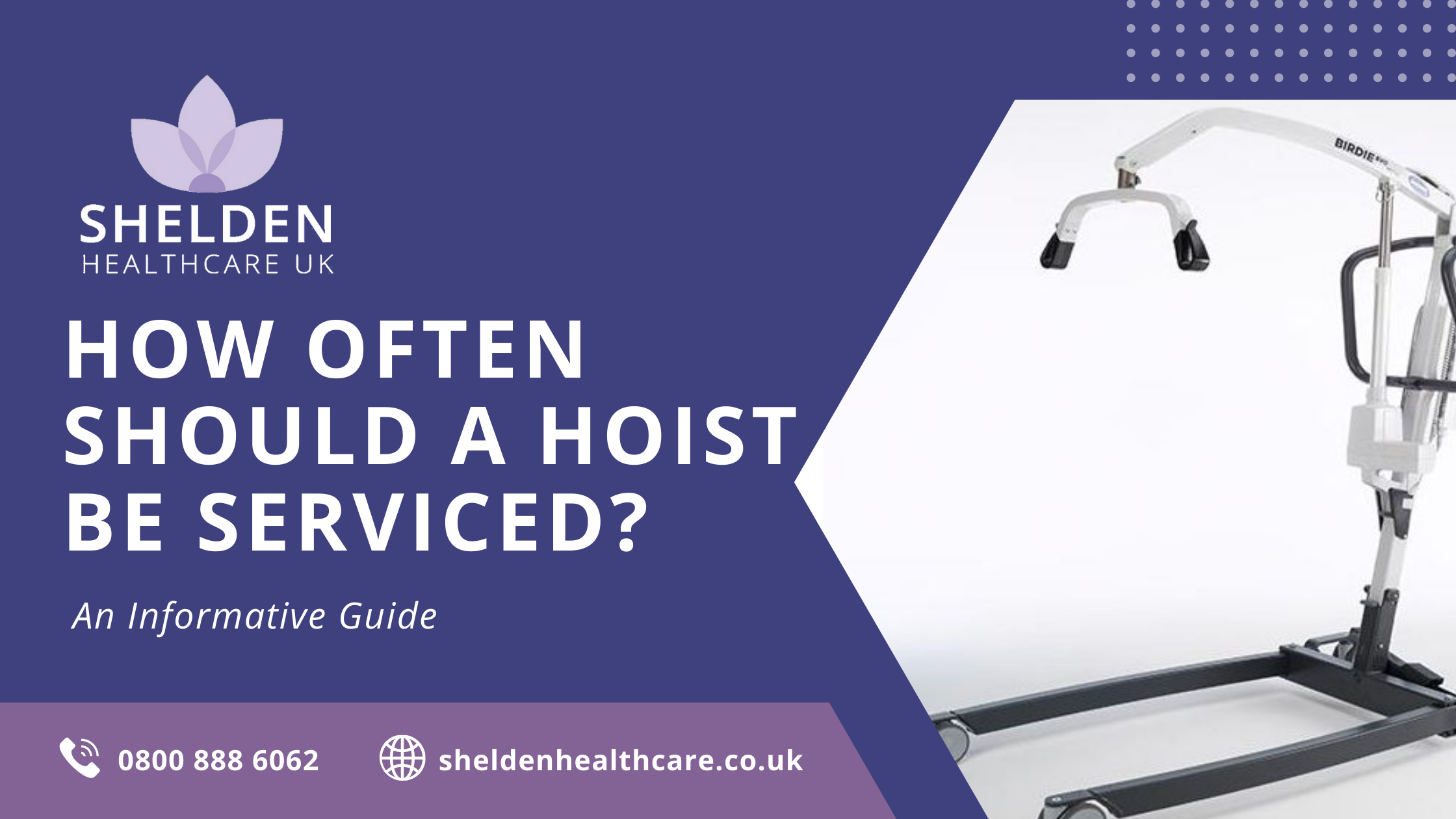
Hoist lifting regulations exist to protect the safety of workers, patients, and bystanders. Companies and individuals have to perform maintenance and examinations of lifting equipment to prevent accidents.
There are several regulations you should know about work equipment. We'll go over each one, explaining the legal and practical requirements for servicing a hoist.
Hoist Lifting Regulations You Should Be Aware Of
The following regulations aren’t mutually exclusive. Your hoisting equipment is probably subject to several regulation categories.
1) H&SWA
The Health and Safety at Work Act (1974), or HASAWA as it’s sometimes called, concerns overall occupational health and safety in Great Britain.
The H&SWA contains general guidelines regarding basic occupational safety, including responsibilities that:
- Employers have towards their employees and the public
- Employees have to themselves and each other
- Self-employed workers have towards themselves and others
2) PUWER
The Provision and Use of Work Equipment Regulations (1998) forces all companies or people who own work equipment, to abide by a set of rules.
PUWER ensures that people who operate and maintain equipment have the required knowledge and understanding of said equipment. It also ensures the presence of required emergency stop devices and protection.
3) MHOR
Manual Handling Operations Regulations (1992) pertain to employers and employees. These aren’t optional guidelines - they’re legal obligations.
Employers have to make adequate assessments of risks that employees will face handling loads. This includes all manual handling tasks. MHOR defines manual handling as:
“…any transporting or supporting of a load (including the lifting, putting down, pushing, pulling, carrying or moving thereof) by hand or bodily force.”
A load in this case can be an object or a person.
Employees are responsible for their personal health, as well as the health and safety of anyone who could be affected by their actions.
Both parties have to confirm that they will fulfil all safety requirements.
4) LOLER
The Lifting Operations and Lifting Equipment Regulations (1998) are the last group of guidelines we’ll be looking at. They’re also the most important ones to consider regarding hoisting equipment.
Because of that, the following segment deals exclusively with LOLER.
The LOLER Inspection
LOLER applies to all businesses and individuals that work with any kind of lifting equipment. Whether someone personally owns said equipment or not doesn’t matter. As long as you or anyone in your workplace operates lifting equipment (e.g., for moving heavy workloads or hoisting patients), you have to abide by LOLER. There are exceptions to LOLER, which we’ll cover later.
In the majority of cases, all lifting equipment is also considered work equipment. As such, it’s subject to PUWER as well.
As we’ve explained beforehand, you need a competent person to perform thorough examinations and oversee the use of all lifting equipment.
What Constitutes A ‘Competent Person’?
Here’s what the LOLER Approved Code of Practice states about finding a competent person:
‘You should ensure that the person carrying out a thorough examination has such appropriate practical and theoretical knowledge and experience of the lifting equipment to be thoroughly examined as will enable them to detect defects or weaknesses and to assess their importance in relation to the safety and continued use of the lifting equipment.’
To put it simply - you need someone reliable and experienced with lifting equipment. As you can see, there are no legal qualifications per see. But the competent person carrying out examinations should be able to quickly identify any flaws or defects regarding said equipment.
Competent persons can come from another organization, and even from within your own company. In-house competent persons are less common, however, since you need someone fully impartial to make crucial assessments.
Whether you choose someone from your company or a third party, please note the following:
The person conducting the thorough examinations should not be the same person that performs routine maintenance of the equipment. They would be assessing their own work in such cases.
The competent person also prepares a Written Scheme of Examination - which shows future scheduled examinations.
Thorough Examinations (TEs)
There’s a difference between a thorough examination and get your equipment serviced.
A competent person has to assess the safety of each part of the lifting equipment and inspects whether everything works properly. These detailed assessments are called thorough examinations.
In other words, TEs are only reports of the state of lifting equipment. Here’s a list of all the information that these reports have to contain.
TEs are done based on specified intervals. The intervals are most commonly - but not always - every six months. You can always find the next scheduled examination within the LOLER report.
At some point, the person performing the examination will find parts of equipment which are not fully up to par, or outright defective. In this case, the designated competent person has to verbally report all defects to the owner.
After the verbal report comes the official written report that contains all relevant information about the lifting equipment defects.
The official report comes in at least two copies:
- one for the owner or company which owns the equipment
- one that is sent to the proper authority
How Often Should You Conduct Thorough Examinations?
Making sure your lifting equipment meets all security standards start from day one.
If said lifting (or handling) equipment was assembled within the workplace, a competent person has to examine it on-site before use. This ensures that everything was installed correctly and that all safety requirements are in check.
This, however, often refers to industrial lifting equipment. But if you’re handling patients, you still want to make sure everything is in place and secure before each use.
Any equipment that’s exposed to conditions can have minute changes that accumulate over time. If you’re using hoist equipment under high heat or cold, certain parts could expand or contract, leading to possible safety risks.
To mitigate these risks, you have to perform regular examinations, which are in this case separate from formal TEs.
LOLER specifies the interval for required TEs between six to twelve months. This goes for most lifting equipment, but hoists should be serviced sooner rather than later.
If the hoisting equipment has been out of use for a long time, a competent person has to perform an examination to ensure the safety of future use.
And finally, any situation where lifting equipment gets damaged or receives modifications and changes call for a thorough examination.
Failing To Comply With LOLER
Breaching LOLER regulations harms you and your business in two ways:
- Not complying with LOLER leads to less secure environments for anyone near the lifting equipment, especially mobile hoists
- You will be liable to massive fines
In 2014 and 2015, a coach company in Wrexham continuously failed to meet LOLER safety standards. After doing so, the company received a £250,000 fine - plus additional costs - from the Wrexham Magistrates’ Court.
No one was harmed due to the aforementioned breach of safety regulations. But the company still received a fine due to the risk alone.
And due to the changes in regime, the Magistrates’ Court can now issue a fine of any amount.
A more drastic example happened in 2012 when two men fell 28 metres from a basket. One of the workers didn’t survive the fall, while the other sustained severe injuries.
The incident happened due to incorrect TEs and repairs. Apart from the imprisonment of the responsible company’s manager, two companies received due to:
- Failure of proper maintenance
- Failure to carry out proper TEs
The total fines exceeded £750,000.
LOLER Exceptions
The LOLER definition of lifting equipment is wide, and as such, it incorporates hoists, ramps, and other lifting equipment.
There are exceptions to it, however. Namely:
- Lifting equipment used on ships
- Lifting equipment labelled by a Declaration of Conformity.
LOLER excludes ship-related lifting equipment because of The Memorandum of Understanding (MoU) between:
- The Health and Safety Executive (HSE),
- Marine Accident Investigation Branch (MAIB), and
- Maritime and Coastguard Agency (MCA).
This memorandum determines the common lines of action between these institutions regarding safety breaches.
The following part relieves equipment owners of the thorough examination only prior to initial use, not regular assessments:
A wide array of lifting equipment will go through conformity assessment prior to entering the market. Because of that, it comes with a Declaration of Conformity (DoC). A DoC confirms a product’s compliance with essential health and safety regulations by the manufacturer.
As such, equipment that comes with a DoC may not require thorough examination prior to its first usage. It only requires a thorough examination if the installation or assembly of the equipment has an effect on its safety and integrity.
What Counts As Lifting Equipment?
Similar to MHOR, LOLER defines lifting equipment as "...any work equipment for lifting and lowering loads."
All lifting equipment has to be designated with a SWL (Safe Working Load) mark. The SWL mark denotes the maximum load that lifting equipment can safely fit
What Are Lifting Accessories?
The HSE describes lifting accessories as pieces of equipment that connect the load to the lifting equipment. This can include, but is not limited to:
- Eyebolts
- Chains
- Slings
- Hooks
See more examples of lifting equipment and accessories in the LOLER Approved Code of Practice and Guidance.
Hoist Regulation for Healthcare Professionals
As we’ve mentioned before, there’s a difference between hoist servicing and performing LOLER tests
Patient lifting equipment needs a full service once per year. This is a legal obligation, and is crucial for any ceiling track hoist system or similar equipment. LOLER test for patient lifting hoists specifically should be done every six months.
The health institution in which the patient resides takes responsibility for the maintenance and testing of every hoist unit on site.
Considering the very delicate nature of healthcare professionals, it's best not to delay any scheduled maintenance work and inspection.
How Often Should A Hoist Be Serviced - Summary
To round things up:
- You should service all hoists and lifting equipment at least once a year, and perform a LOLER inspection every six to twelve months
- Competent persons can do a visual examination of core equipment and accessories, in search of light and serious defects. This is called a thorough examination.
- The competent person has to immediately report any defects found and schedule the next thorough examination date.
- Healthcare institutions work with patient hoists that need constant checkups and should perform TEs sooner rather than later, as to avoid any emergency incidents.